Il manuale della apparecchiatura è l’unico documento di riferimento per tutte le norme di sicurezza. Solo il personale qualificato può operare sull’inverter.
Di seguito una guida veloce per l’installazione, tutte le operazioni possono essere svolte da tastiera, ma è sempre consigliato l’utilizzo del programma programma INVT Workshop.
Tutte le configurazioni descritte in questo articolo si riferiscono ad una condizione dell’inverter di default, come prima operazione impostare tutti i parametri dell’inverter a default, settare P00.18=1.
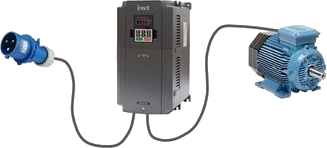
Approfondimenti
- In questo topic video su procedura cambio lingua menù da Cinese ad Inglese.
Connessioni elettriche
Una descrizione dettagliata delle connessioni elettriche è riportata nel manuale dell’inverter, ma riportiamo alcune informazioni per evitare gli errori più comuni:
- Il teleruttore di sezionamento potenza trifase deve essere connesso sulla alimentazione dell’inverter e non sulla uscita verso il motore.
- Eventualmente è possibile evitare il teleruttore agendo sul comando STO che evita una partenza inaspettata o effettua un arresto sicuro.
- Occorre agire sul teleruttore o sullo STO solo a motore fermo. L’apertura del teleruttore o del circuito STO con inverter in funzione è da limitarsi unicamente alle condizioni di emergenza.
- Installare il filtro in uscita all’inverter verso il motore negli inverter.
Gestione 2 motori
L’inverter ha la possibilità di gestire 2 diversi motori (Di default è attivo il motore 1), tramite teleruttori è possibile eseguire lo scambio della connessione in uscita sui 2 motori. Lo scambio và effettuato a motore fermo ed inverter disabilitato. La selezione del motore attivo è definibile dal parametro P08.31 (Default 0) che abilita selezione da ingresso logico, consiglio di utilizzare l’ingresso S4 impostando il parametro P05.04=35. Per l’impostazione dei parametri motore all’interno dell’inverter sono previsti due gruppi di parametri.
- P02.xx per i parametri del motore 1
- P12.xx per i parametri del motore 2
Autotuning motore
Eseguito il collegamento di tutti i componenti filtro di rete, motore, resistenza di frenatura collegando l’inverter alla rete per prima cosa dobbiamo impostare i parametri del motore. Esistono 2 procedure di autotuning dinamica da eseguire con il motore disaccoppiato dal carico, statica eseguibile con il motore accoppiato al carico, se possibile è preferibile eseguire la procedura dinamica.
- Definire parametri motore, Potenza P02/P12.01, Frequenza nominale P02/12.02, Velocità rotazione P02/12.03, Tensione P02/12.04, Corrente P02/12.05. Tutti gli altri parametri sono calcolati automaticamente dalla procedura di autotuning.
- Abilitare i comandi da tastiera P00.01=0. In questo modo è attiva la tastiera dell’inverter.
- Attivazione autotuning P00.15 l’autotuning verrà eseguito sul motore selezionato.
0: Nessuna operazione
1: Autotune dinamico dei parametri motore completo.
Si consiglia di utilizzarlo quando è necessaria un’accuratezza di controllo elevata ed il motore può essere fisicamente separato dal carico.
2: Autotune statico dei parametri motore completo.
Da utilizzare quando il motore non può essere separato dal carico.
3: Autotuning statico dei parametri motore parziale.
Tuning solo dei parametri P0/12.06, P02/12.07, P02/12.08 - Attivando l’autotuning sul display apparirà la scritta lampeggiante -run-, agendo sul comando [RUN] verrà effettuata la procedura (Se si è scelto la procedura dinamica il motore andrà in rotazione) e sul display apparirà un numero progressivo dopo la scritta -run-x. Terminata la procedura l’inverter andrà in stop.
Resistenza di frenatura
Gli inverter fino alla potenza di 37Kw dispongono di unità di frenatura interna, per le taglie superiori occorre utilizzare l’unità di frenatura esterna, occorre comunque abbinare una resistenza di frenatura adeguata all’impiego. Come si vede nella tabella per ogni taglia esiste un valore tipico di resistenza per frenatura al 100% della coppia motore, ed un valore minimo sotto al quale si danneggia l’unità di frenatura.
Sono riportati 3 valori di potenza (Espressi in Kw) a cui dimensionare la resistenza in base alla “rapidità” di frenatura che si vuole ottenere, i valori sono riferiti ad un rapporto di utilizzo del freno del 10%.
In generale questi valori di potenza sono estremamente cautelativi, noi solitamente consigliamo una potenza superiore al 10% della potenza dell’inverter. Ad esempio per un inverter da 7.5Kw consigliamo una resistenza da 60Ohm ed una potenza di almeno 800W. Poi naturalmente se l’impegno in frenata è molto gravoso sia come “rapidità” di frenata e/o interventi di frenatura ravvicinati, occorre considerare una potenza superiore.
Connessa la resistenza occorre abilitarne il funzionamento settando a 1 il parametro P08.37 Energy consumption brake enable. Il parametro P08.38 Energy consumption brake threshold voltage, permette di impostare la tensione sul bus in continua a cui si attiva la resistenza di frenatura. Il valore và impostato in base alla tensione di alimentazione dell’inverter per inverter a 220V il valore da impostare e 380V per inverter a 380V il valore da impostare è 700V.
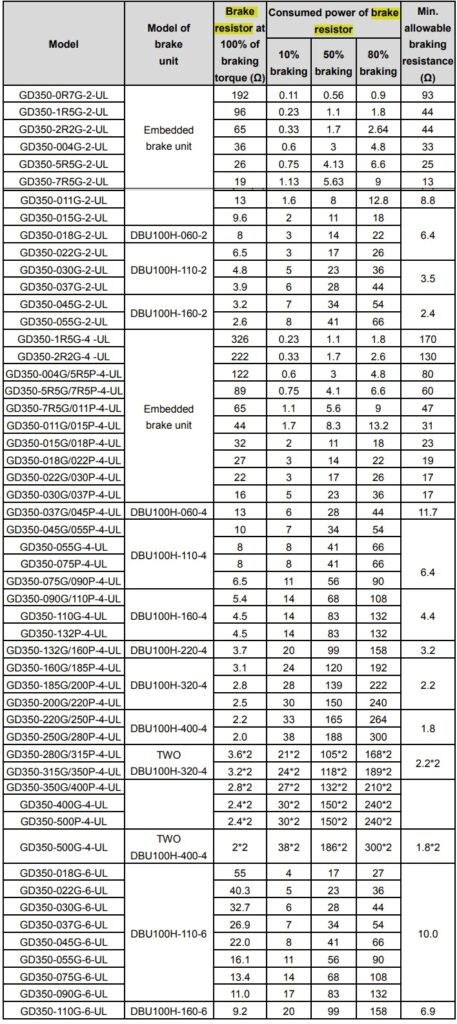
Configurazione inverter
Configurando i vari parametri dell’inverter è possibile ottenere moltissime configurazioni di utilizzo, di seguito le configurazioni più utilizzate.
Configurazione interfaccia ethernet ModbusTCP
E’ disponibile la scheda EC TX515 con interfaccia ethernet per il supporto al protocollo ModbusTCP. La scheda và montata ad inverter spento su uno degli slot disponibili, la posizione non influisce con il funzionamento, se libero si consiglia lo slot 1.
- Verificare con il parametro P19.00 (Slot1), P19.01 (Slot2), P19.02 (Slot3), se la scheda è stata riconosciuta dall’inverter, P19.00=16: Modbus communication card.
- Verificare con parametro P07.13 la versione firmware dell’inverter. Le impostazioni parametri IP scheda sono riferite a versioni da 3.02.xx.
Impostare indirizzo IP parametri da P16.58 a P16-61.
Impostare mask parametri da P16.62 a P16-65.
Impostare gateway parametri da P16.66 a P16-69. - Impostare indirizzo Modbus, P14.00=xxx.
- Impostare protocollo Modbus, P00.02=0.
- Impostare controllo da protocollo Modbus, P00.01=2.
- Selezionare comando di frequenza A con impostazione da Modbus P00.06=8.
- Selezionare come sorgente di velocità il comando di frequenza A P00.09=0.
Regolazione PID da ingresso analogico
In questo modo operativo è possibile gestire una retroazione PID su di un valore di setpoint impostato. Per configurare questo modo operativo occorre:
- Impostare controllo motore in V/F, P00.00=2.
- Abilitare comando rotazione da ingressi digitali, P00.01=1.
- Impostare frequenza massima assoluta, P00.03=xx.
- Impostare frequenza massima di lavoro, P00.04=xx.
- Impostare frequenza minima di lavoro, P00.05=xx.
- Impostare come Frequency command selection, l’uscita della funzione PID, P00.06=7.
- Selezionare comando di marcia avanti da ingresso S1, P05.01=1.
- Selezionare l’ingresso di set point PID reference source, P09.00=xx.
- Impostare come PID feedback source l’ingresso di feedback del PID, P09.02=xx.
Considerazioni
- Se P09.00=0 come valore di set point del PID viene considerato il parametro P09.01 (In percentuale da -100% a +100%) che è impostabile da tastiera.
- Per avere il feedback del PID da un sensore analogico è possibile impostare P09.02=0 in tal caso viene utilizzato l’ingresso analogico AI1.
- Per utilizzare l’ingresso AI1 con un sensore 4-20mA occorre impostare P05.50=1 AI1 input signal type in current type. Occorre tenere presente che anche in corrente il valore sarà interpretato in volt nel range 0-10V (4mA corrispondono a 2V).
- E’ possibile impostare i limiti basso/alto di AI1, P05.24 Lower limit value, P05.25 Corresponding setting, P05.26 Upper limit value, P05.27 Corresponding setting. P17.19 visualizza in tempo reale il valore in volt dell’ingresso AI1.
- Rampa accelerazione con funzionamento da PID: L’uscita del PID comanda la velocità motore subordinatamente ai parametri di rampa P00.11, P00.12. Ma l’uscita PID assume di iniziare il comando da velocità 0 e non da velocità minima, è possibile comunque in P09.09 e P09.10 definire la percentuale di velocità in cui deve operare il PID.
Esempio applicazione
Comando pompa con traduttore di pressione 0-20mA connesso ad ingresso analogico AI1 con range 0-10Bar. Impostare
- P05.24=0V, P05.25=0%, P05.26=10V, P05.27=100%, così l’ingresso di feedback del PID avrà valore 0-100% nel range 0-10Bar. Se il trasduttore avesse range 4-20mA dovremmo impostare P05.24=2V, P05.25=0%.
- Siccome l’uscita del PID regolerà la frequenza sarà possibile impostare il set point di pressione in P09.01 e visto che impostando 100% il PID gestirà il motore per avere il 100 in feedback il valore impostato varrà Bar/10. Quindi impostando 50 avremo la regolazione su 5Bar.
- Utilizzo autoclave: Alla chiusura dell’utenza la pressione sale e l’inverter deve arrestarsi quindi: P01.19=0x12, in questo modo dopo il tempo definito il P1.34 in cui l’inverter comanda il motore alla velocità minima P00.05 và in condizione di sleep. Appena la pressione scende ed il PID setta una frequenza superiore al minimo l’inverter riparte.